News & events
In this section you will find all the latest news of the Danieli Group. Selecting the categories below, you can see News, Records, Start-ups, New Orders.
top performances
2017, 4th October
Technology and manufacturing
Day 2 at Fourth Danieli Innovaction Meeting
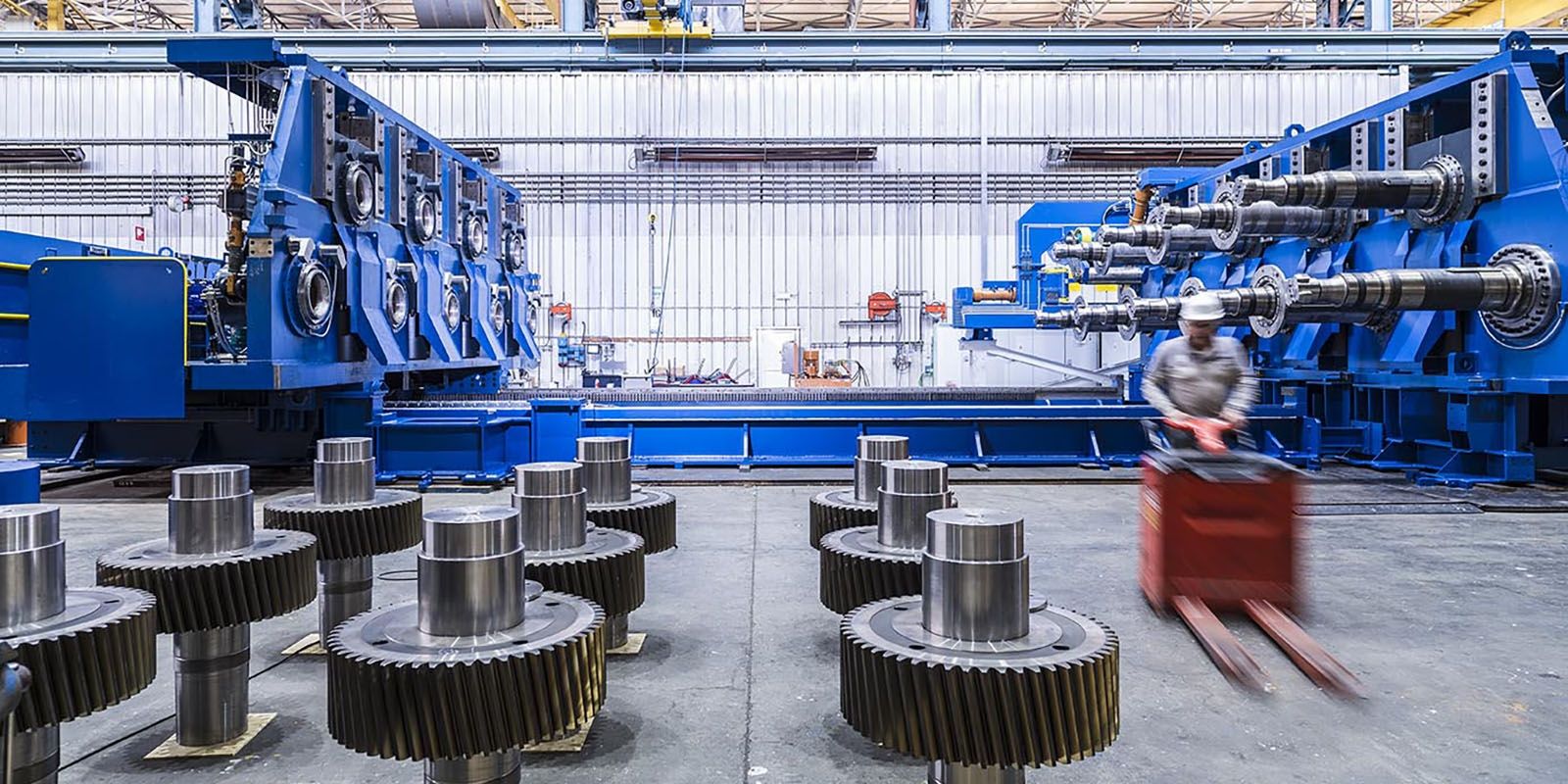
Day 2 of Danieli Innovaction Meeting 2017 began with a visit to the workshops at Group Headquarters in Italy. There, with a guided tour by technological experts, the 600 guests to this week’s events viewed exhibits of some major workshop projects for key customers. Among these we mention:
The most notable machine on display was the JUMBO Straightener, now completing testing prior to shipment to ArcelorMittal. With nine double-supported rolls designed to straighten cold steel sections with modulus up to 3800cm3, and with a variable roller pitch from 2700 to 2300mm, it is the largest in the world.
A particularly noteworthy exhibit were segments 0 and 7 for a new slab caster in development for VA Stahl in Linz, Austria. Also shown were the FastCast cube of a new high-speed billet casting machine, for high-productivity steelmaking plants and endless rolling.
The DANCU (Danieli Charghing Unit) was shown in testing: the Danieli original solution optimizes material distribution with a rotating layering system inside a blast furnace, replacing the bell solution.
A “Carousel” coiler was shown for a fully continuous tandem cold rolling mill, with two independent re-coilers mounted on a “revolver” that will be able to rotate around its axle without interruption for coil wrapping.
Several examples of equipment refurbishing also attracted the attention of the visitors. These included a family of HAGC hydraulic capsules for controling strip thickness in hot strip mills with up to 6000 t force.
A wide series of new and resurbished bushings for oilfilm bearings for hot and flat product mills were presented, during the maching stages and as finished products prior to shipping.
Danieli HQ workshop is the exclusive location for producing and testing the fast finishing blocks for all rolling mills and gear boxes supplied worldwide, for the production of wirerod at up to 140 m/sec.
A fascinating grinder mill was exhibited. The machine is designed to reduce the size of light scrap, altering the granulometry of the intake material to produce sortable fractions.
These exhibits were shown along with many other “standard” machines now in production at the HQ workshops for steelmaking, long, flat, tubular and extruded products plants and equipment, being supplied to Danieli customers around the world.
Group HQ workshops are equipped with the most modern CNC milling, boring and grinding machines. Gear cutting and heat treating are a distinguishing capabilities of the workshop. It also offers specialized fabrication processes, such as narrow gap welding on materials up to 1000 mm thick.
Following the workshop tours, guests proceeded to seven presentations and discussions of various production technologies of their specific interest. These were detailed explanations of proven and emerging Danieli technologies for Iron and steelmaking, EAF meltshop and casting, flat products, long products, aluminium and nonferruous metals, and tube, pipe, forging and extrusion plants.
The day concluded with a presentation of the Danieli Group financial results for 2016/2017, with elaboration and commentary by all of the Group’s leaders.