News & events
In this section you will find all the latest news of the Danieli Group. Selecting the categories below, you can see News, Records, Start-ups, New Orders.
top performances
2017, 13th October
Developing effective solutions for demanding markets
The tube and pipe plants, forging and steel extrusion sessions of the Fourth Danieli Innovaction Meeting
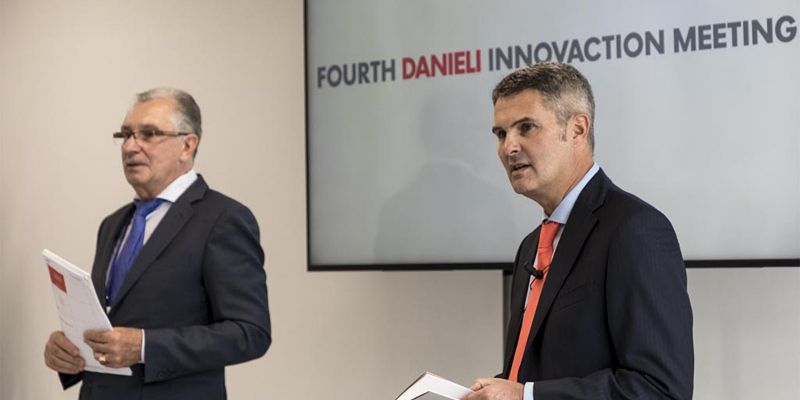
Highly specialized engineering requirements in the tube and pipe market create the possibility for suppliers of tubular products, and extrusions to establish a unique market presence, and for this they must have timely insights, advanced production technologies, and new integrated plant concepts. Guests attending the tube and pipe plants, forging and steel extrusion session at the Fourth Danieli Innovaction Meeting took in all of these.
The session opened with a detailed market analysis of seamless tube and welded pipe market by James Ley and Roman Filimov from Metal Bulletin. Good news:
> The global OCTG market (seamless and welded) is showing a rebound from the low level of 2016 for production and demand, with forecast remaining positive.
> The large diameter pipes demand (LSAW and HSAW) is foreseen to have a gradually grown, more significant for the HSAW Plants.
At the end of the presentation, Philip Carlier (Senior VP -Member of the Group executive Committee) from Vallourec - France and Alexander Klachkov (Deputy General Director and Chief Eng.) from TMK- Russia, joined Metal Bulletin specialist for a discussion panel.
Several aspects of the tube market scenario have been deeply analyzed and discussed, with special focus on the role of the plant supplier, as Danieli. The main indications have been to study and develop plant configurations permitting:
> Closer tolerances
> Capability to process a wider variety of steel grades
> Improve plant yield
> High flexibility in production campaigns (to match small lots of production)
> Easy operation and maintenance (to compensate lack of qualified people and/or speed up training of un-experienced people)
All the above with the final target to be top level quality producer and have competitive production costs.
Moreover, concepts of energy savings shall be considered.
Furthermore, during Q&A time that accompanied all the technological presentations, it become clear that the open and close die forging industry is showing development on aerospace sector, especially for engine applications in nickel based materials and aluminum.
As far as the steel extrusion is concerned, the market is stable for the more traditional applications while is showing some development in India, China and Korea, in connection with local programs on nuclear power generation.
Concerning the presented topics:
“Tube market analysis. Discussion panel” took the perspective that oil prices are recovering and demand for new, high-specification pipes is reviving the industry. So, now is the time to be proactive and to focus on commercial and technical issues in the OCTG and line pipe market. The Metal Bulletin team provided an analysis of the global and regional demand drivers for oil-and-gas and pipeline projects, and an outlook into worldwide steel tube and pipe situation, underlining not only actual situation and future movements but also relevant impacts on market.
“Tube & pipe discussion panel,” including experts from Metal Bulletin, followed the tube market analysis with views from delegates representing the main global tube and pipe manufacturers discussing the market outlook, plus relevant topics in market trends, threats and opportunities.
“Seamless tube plants overview” began with a historical view starting in 2004, when Danieli Centro Tube entered the fast-growing seamless pipe plant market with innovative technologies and a complete product line. DCT’s continuous activity in technology innovation and development ensures it remains one-step ahead, enabling it to make considerable contributions to customers’ efforts to obtain ever-higher product quality at lower transformation costs. The results achieved by Danieli Centro Tube confirm the leadership and the capability of Danieli Group in advanced technology, research and product development, offering plants for hot rolling and cold finishing for seamless pipes that fulfill the most demanding applications in terms of quality and quantity.
“Latest technologies for competitive and quality seamless tube production” considered the most recent Danieli seamless pipe rolling innovations, namely Fine Quality Train (FQT) and Hot Pull Elongator (HPE), which combine top quality results with reduced CapEx and OpEx, starting from 100-kton/year capacity requirements. Covering different product ranges and based on different rolling technologies, FQT and HPE together provide Danieli customers with compact and flexible solutions for producing pipes ranging from 7/8” to 16-¾”, even in single-piece lots, and at the most competitive costs serving both global and local markets. These new technologies are designed to be compact, and also can be implemented as revamps.
“Smart maintenance: a flexible, cost-effective tool for improved plant reliability,” started by considering that, "the basic principle of the Fourth Industrial Revolution is that communication and the symbiosis of individual, specialized components work effectively to achieve a greater overall result". Following this, Danieli is addressing its concept of smart maintenance, where equipment is born or can be retrofitted with devices so that it is ready to interact in the smart factory. Flexibility, openness and the use of best-in-class technologies are the driving forces of Danieli Digi&Met Smart Maintenance, which is one of the digital-enabling technologies for the smart factory.
“Welded tube plants overview” studied the challenging market situation that requires an equipment designer and manufacturer like Danieli W+K to significantly change its approach to customer needs. It is essential to anticipate market trends and develop new innovative, technological solutions, in order to increase business profitability. The outstanding experience in HSAW and ERW plants for welded pipes, as well as special equipment for OCTG premium connections and CRA (Corrosion Resistance Alloys) products, create the possibility to establish very effective, win-win cooperation with customers based on effective tube manufacturing process knowledge.
“Premium coupling threading machine and cold pilgering technology” identified the highly demanding aerospace, nuclear, automotive and OCTG sectors in which special-quality premium tubular product consumption is growing. The extremely rigid, continuous QUARTO cold pilger line is a high-productivity mill capable of producing zirconium precision tubes and bars at high speeds in tight dimensional tolerances (OD ±0.2%, WT ±3%, flatness 0.020 mm, waviness 0.020 mm). For 28Cr OCTG CRA pipes, non-continuous DUO cold pilgering ensures high separating forces, 50% more than competing system designs. The Premium Coupling Threading machine’s simultaneous push-and-pull threading and automatic loading and unloading is ideal for high-speed threading of API connections (22 pcs/h for 7” API Buttress P110) and high-precision threading of premium connections (10 pcs/h for 7” typical P110 T&C premium.)
“Forging plants overview,” detailed the progress made by Danieli Breda since 1950 as it defined and developed the state-of-the-art for the forging industry. Being always one step ahead, Danieli Breda always keeps in mind technological improvements and forging process optimization. The technological packages it offers are aimed at increasing plant efficiency and productivity. The Virtual Inertia Drive power management allows reducing the installed power up to 60%. The contactless measurement systems ensure fast, reliable and precise real-time measurement of forged pieces. Finally, our DanForge Automation System, a totally integrated automation system for complete forging plants, is capable of managing the entire forging process in complete automatic mode.
“A competitive railway axle complex” described one of the most innovative, compact, flexible and cost-oriented axle forging plant on the market, developed by Danieli Breda and based on flexibility, cost optimization and environmental sustainability. It is designed to process billets of different shapes, offering a remarkable wide flexibility on the feedstock. The compact design allows 60% savings in plant footprint, and the adoption of energy-efficient systems reduce energy consumption by more than 35%, ensuring very low transformation costs. The overall initial investment is 50% of a traditional radial forging plant, leading to a shorter ROI.
“A complete plant, from extrusion through finished pipe” proposed a pipe mill concept to address OCTG market opportunities for unconventional resources, like shale gas, shale oil and tight sands. These require sophisticated materials such as CRA (Corrosion Resistant Alloys), carbon steel with enhanced Sour Service Performance, or martensitic grades (13Cr and Super 13Cr). Danieli Group draws on long expertise backed by diverse, in-house product lines: Danieli Breda for hot extrusion, Danieli W+K for cold pilgering and threading machines, Danieli Centro Maskin for drawing together with Danieli Centro Tube’s expertise in straightening, hydrotesting and NDT testing.
“High-tech pipe tempering furnaces for increased capacity and uniform temperature across the products” offered comparisons between a CFD model of a recent installation of a pipe tempering furnace and results of performance tests on site, in terms of temperature uniformity. To perform this task efficiently and ensure excellent temperature uniformity, the furnace has a radiant section on the entry side, where direct-flame burners and a convection section, including a fume recirculation system, are installed. A new furnace design concept with direct- and indirect-firing configurations matches the layout constraints and achieves thermal uniformity. Direct firing is applied in the heating zone and indirect firing in the soaking zone. The combustion chamber applies high recirculation to improve heat exchange of the convection type.