News & events
In this section you will find all the latest news of the Danieli Group. Selecting the categories below, you can see News, Records, Start-ups, New Orders.
top performances
2017, 12th October
Developments for energy savings and flexibility
The iron and steel session of the Fourth Danieli Innovaction Meeting
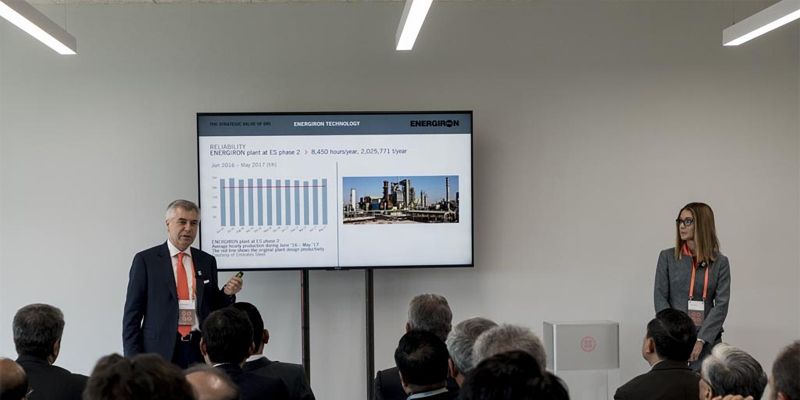
Iron and Steelmaking operations must incorporate the latest available insights regarding cost savings, process flexibility, and energy conservation, just to list some of the most important goals. Guests who attended the Iron and Steel session at the Fourth Danieli Innovaction Meeting were able to consider several technologies in this way. The topics covered included:
“Beneficiation plants and pelletizing technology: OpEx reduction and sustainability” traced the expansion of the upstream expansion since 2000 of the Danieli portfolio of iron and steel industry technologies into Iron Ore Processing plants. In recent years, several solutions have been implemented to improve OpEx and sustainability of these plants. The most relevant result is the water-conserving technology for beneficiation plants, a fully automated pelletizing pot grate that determines the best operating parameters for increasing productivity and product quality; the reduction of NOx emissions and fines generation; as well as optimization of plant feed material by waste recycling in pelletizing.
“Q3 Intelligence: automation to reduce production cost for DRI process,” explained how the New Normal market situation requires a new vision for steelmaking, one that emphasizes flexibility, reliability and environmental care are the keywords for success. The ENERGIRON DRI process, coupled with the EAF-based mini-mills is an alternative to the blast furnace route, as demonstrated by the most recent results. The need for constant quality, flexible quantity and quickness based on market needs, calls for advanced automation systems to support operators and managers. The answer to this challenge is Danieli’s “Q3 Intelligence” automation system for the ENERGIRON Direct Reduction Plant.
“Environmental solutions for a sustainable industry,” considered how metal producers industries must consider environmental technologies as integrated parts of the core metallurgical process. Danieli is focusing on Zero Emission and Total Recycling technologies, to fulfill the GREEN VISION by: 1) Reducing plant OpEx, in order to offset the effects of “polluter pays” principle; and, 2) Gaining sustainability certification for final products. The first competitor to apply these concepts will take advantage and overcome the challenges of the New Normal period.
“Give water a second life: municipal wastewater for industrial water applications,” described the Danieli solution for wastewater reuse by reducing or zeroing the demand of primary water. These plants provide an effective-zero environmental impact on surrounding water ecosystems by combining the reuse of treated municipal wastewaters and zero liquid- discharge technologies. Waste is given a new economic value by applying dedicated business models between public and private sectors, modern concepts of sharing the responsibilities and benefits for a sustainable use of natural resources.
“Tailor-made energy monitoring and optimization” considered how increases in energy efficiency are not dictated only by government policies but by the need to reduce production costs and improve competitiveness. Measuring actual energy consumption is the starting point for a smart plant, in line with Industry 4.0 standards, and the Danieli Energy Management System (DEMS) was conceived specifically for energy monitoring and consumption control for metals production, with easy connectivity to any existing system and availability of cloud service. This software system and its analysis tools can identify possible areas for improved energy efficiency, and more than 20% of the electric consumption for a process area can be optimized.
“Modern blast furnace design: fit-for-purpose campaign strategies,” evaluated how blast furnaces must cope with the increasing demand for higher coal injection levels, lower quality raw materials and fluctuations in production. Now, furnaces should be designed to achieve the targeted campaign lengths at an availability of over 95 %. The Danieli Corus bosh and stack design based on copper-plate cooling and high conductivity graphite is the only design for which the capability to achieve campaign lives of over 25 years is beyond debate. A method for modular conversion of existing, stave–cooled furnaces to plate cooling will allow such a conversion in around 40 days.
“Hot blast stove campaign extension: smart approaches to postponing capital projects,” was a review of the developments that have extended campaigns to over 30 years, without major repairs. Some stoves are currently close to the 50 years in Europe and North America. Repairs to subsystems such as burners and hot blast outlets may be required. Depending on a plant’s production capacity, these repairs may have to take place in the shortest possible timeframe to minimize production loss. Danieli Corus presents an approach for intermediate repairs, executed while keeping the majority of the system at operating temperature.
“Blast furnace top charging technology: the new standard in reliability and maintainability,” described the Danieli Top Charging Unit with DANCU distributor, fabricated with the highest quality standards and offering maximum up-time, with minimal manpower requirements for operation and maintenance. The design based on hydraulic top-charging, with the distributor having few moving parts, is the most straightforward, robust design available. All the main components are failure–free or redundant. It is a full–scale system based on a new maintenance concept: all key equipment and components are positioned on rail systems, so that they can be removed and re–installed in minimum time.
“Blast furnace gas cleaning technology: dry and wet solutions for substantial energy savings,” is a summary of the Danieli Corus dry gas-cleaning system based on proven technology. It consists of a gas conditioning tower, reagent injection system and bag filter modules with low-pressure pulse cleaning. The system was designed for a residual dust content below 5 mg/Nm³, increased TRT output and calorific value of the blast furnace gas.
For wet blast furnace gas-cleaning, Danieli Corus introduced a replacement demister, with smaller footprint, 99.96 % removal efficiency, and a higher calorific value of the blast furnace gas.
“Optimized BOF revampings: improved process efficiency and equipment monitoring” reported on the growing demand to optimize existing plants, to reduce OpEx and increase safety for operators. And so, the current program for converter design calls for increasing the service life of converter core equipment, and minimizing manual activities during operation and maintenance. These are achieved thanks to the Q-Temp temperature monitoring system; the “DANIELLA” maintenance-free suspension system; the Q-Load load-monitoring system; and by enlarging converters to optimize equipment design.
“Advanced skirt design for BOF cooling stacks ‘virtual hood’” explained how the core element in a BOF Cooling Stack is the adjustable skirt. Its design and reliability determines the performance/availability of the whole system. The skirt is located in an extreme environment and is subject to high wear and tear. The typical service life is limited to 15-36 months. Even if the exchange time can match up with scheduled BOF relining periods, unscheduled downtimes are frequently experienced. Danieli developed “virtual hood” overcomes these limitations.
“Allothermic technology for improved BOF steelmaking” explained how “unfired O2-top blowing converter steelmaking has the disadvantage of a limited scrap rate (25%). With the allothermic (fired) top and bottom O2-blowing converter operation, lime-coal powder is injected from the bottom of the converter. With coal-injection, the scrap rate can be increased to 50%, and with scrap preheating to 35-40%. If the scrap rate is increased, e.g. from 230 to 500 kg/t, liquid steel by coal injection up to 450 kWh/t.
“BOF 4.0: advanced automation for highest production savings” described the new Danieli AutoBOF technology for intelligent BOF steelmaking. It consists of high-level automated functions for all the process steps, as well as various control systems. With AutoBOF, there is potential for OpEx savings: at least 15 % fewer operational staff is required and a high level of consistency and repeatability is achieved. This results in optimized material usage, reduced slag carry–over, savings in ladle alloys additions and fewer spills, repairs and delays. Finally, the embedded safety features improve operator safety.